In precision manufacturing, where accuracy and consistency are paramount, air tools have emerged as indispensable assets. These pneumatic marvels offer a unique combination of power, control, and versatility that makes them ideal for a wide range of precision applications. This comprehensive guide will explore the various applications of air tools in precision manufacturing and delve into the numerous advantages they bring to the production floor.
Key Takeaway
Air tools are indispensable in precision manufacturing, offering unparalleled accuracy, consistency, and versatility across various industries. Their precision, safety, and long-term cost-effectiveness advantages make them a crucial component of modern manufacturing processes. As technology advances, air tools will play an even more significant role in pushing the boundaries of precision and efficiency in manufacturing.
The Fundamentals of Air Tools in Precision Manufacturing
Air tools, also known as pneumatic tools, harness the power of compressed air to perform various tasks with high precision and efficiency. In the context of precision manufacturing, these tools offer unparalleled control and consistency, making them invaluable in industries where tolerances are measured in microns.
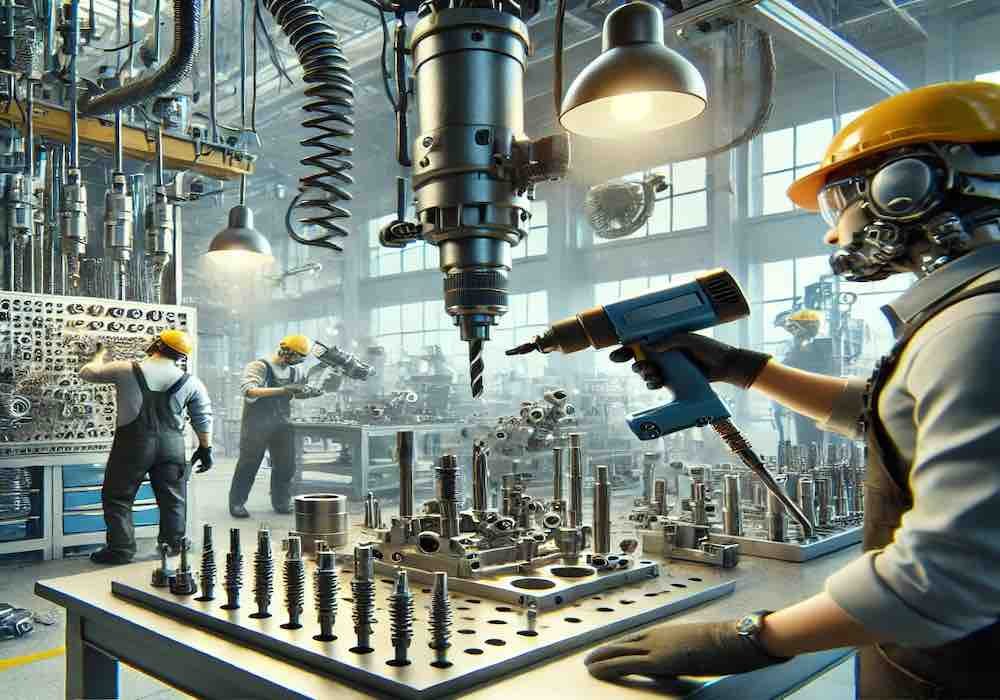
Core Components of Air Tool Systems:
- Air compressor
- Air treatment units (filters, regulators, lubricators)
- Air lines and fittings
- Pneumatic tools (drills, grinders, screwdrivers, etc.)
Applications of Air Tools in Precision Manufacturing
Aerospace Industry
In aerospace manufacturing, where precision is critical for safety and performance, air tools play a vital role:
- High-speed drilling of composite materials
- Precision fastening of aircraft components
- Surface finishing of turbine blades
- Riveting of fuselage panels
Automotive Precision Components
The automotive industry relies heavily on air tools for producing precise components:
- Cylinder honing for engine blocks
- Valve seat grinding
- Precision torque control for assembly
- Fine surface finishing of critical parts
Medical Device Manufacturing
In the medical field, where precision can be a matter of life and death, air tools are essential:
- Micro-drilling of surgical implants
- Precision grinding of prosthetic components
- Assembly of delicate medical devices
- Surface texturing of implantable materials
Electronics and Semiconductor Production
The electronics industry leverages air tools for various precision tasks:
- PCB drilling and routing
- Component placement and soldering
- Precision cleaning of sensitive parts
- Micro-engraving of electronic components
Watchmaking and Jewelry Crafting
These industries require the utmost precision for creating intricate pieces:
- Micro-drilling of watch movements
- Precision engraving of jewelry
- Fine polishing of gemstones
- Delicate assembly of watch components
Optical Lens Manufacturing
Air tools are crucial in producing high-quality lenses for various applications:
- Precision grinding of lens surfaces
- Fine polishing of optical components
- Micro-drilling of frame components
- Assembly of complex optical systems
Advantages of Air Tools in Precision Manufacturing
Exceptional Precision and Control
Air tools offer unparalleled precision due to:
- Adjustable air pressure for fine control
- Consistent power output throughout operation
- Minimal tool deflection under load
This level of control is crucial for maintaining tight tolerances in precision manufacturing.
Reduced Operator Fatigue
Pneumatic tools are generally lighter and more ergonomic than their electric counterparts, leading to:
- Reduced operator fatigue during extended use
- Increased productivity and accuracy
- Lower risk of repetitive strain injuries
Improved Safety
Air tools offer several safety advantages:
- No risk of electric shock in wet environments
- Lower heat generation during operation
- Reduced risk of sparks in explosive atmospheres
This makes them ideal for use in sensitive manufacturing environments.
Cost-Effectiveness
While the initial setup cost may be higher, air tools offer long-term cost benefits:
- Lower maintenance requirements
- Longer tool lifespan
- Reduced energy consumption for certain applications
Versatility and Adaptability
Air tools can be easily adapted for various precision tasks:
- Quick change of tool bits and accessories
- Wide range of speed and torque options
- Ability to work in tight spaces and awkward angles
This versatility makes them invaluable in flexible manufacturing environments.
Cleanliness and Contamination Control
In clean room environments and sensitive manufacturing processes, air tools offer:
- No risk of oil contamination (with oil-free compressors)
- Minimal particle generation during operation
- Easy integration with air filtration systems
Consistent Performance
Unlike electric tools, which can experience power fluctuations, air tools provide:
- Consistent power output regardless of battery charge
- Stable performance in varying temperatures
- Reliable operation over extended periods
This consistency is crucial for maintaining quality in precision manufacturing.
Challenges and Considerations
While air tools offer numerous advantages, there are some considerations to keep in mind:
- Initial Setup Costs Implementing a comprehensive air tool system requires investment in compressors, air treatment units, and distribution systems.
- Noise Levels Proper soundproofing and the use of silent compressors may be necessary to maintain a quiet work environment.
- Air Quality Management Maintaining clean, dry air is crucial for the longevity of tools and the quality of finished products.
- Energy Efficiency Ensuring an efficient compressed air system is essential for minimizing operating costs.
Future Trends in Air Tools for Precision Manufacturing
As technology advances, we can expect to see:
- Integration of IoT for predictive maintenance and performance optimization
- Development of micro-air tools for nano-scale manufacturing
- Advanced materials for lighter and more durable tool construction
- Improved energy efficiency in compressed air generation and distribution
- Enhanced precision control through digital air pressure regulation
FAQs:
- Q: How do air tools maintain precision over long periods of use? A: Air tools maintain precision through consistent power output, minimal heat generation, and reduced vibration compared to electric tools. Regular maintenance and proper air quality management are key to long-term precision.
- Q: Can air tools be used in clean room environments? A: Yes, air tools can be used in clean rooms when paired with proper air filtration systems and oil-free compressors. They generate minimal contaminants during operation, making them suitable for sensitive environments.
- Q: How do air tools compare to electric tools in terms of precision? A: Air tools often offer superior precision due to their consistent power output, finer control over speed and torque, and reduced tool deflection under load. This makes them preferable for many high-precision applications.
- Q: What industries benefit most from using air tools in precision manufacturing? A: Industries that benefit significantly include aerospace, automotive, medical device manufacturing, electronics, watchmaking, and optical lens production. These sectors require extreme precision and consistency in their manufacturing processes.
- Q: Are there any limitations to using air tools in precision manufacturing? A: While air tools excel in many areas, they require a compressed air infrastructure, which can be costly to set up. They also need proper air quality management and may have limitations in extremely cold environments where condensation can be an issue.
For expert guidance on integrating air tools into your precision manufacturing processes, visit pneumatictoolz.com. Our team of specialists can help you select the right air tools and systems to enhance your manufacturing precision and efficiency. Contact us at sales@pneumatictoolz.com for customized solutions and top-quality pneumatic tools.