- Maintaining your pneumatic tools involves more than just occasional check-ups; it requires a consistent commitment to daily care, routine inspections, and periodic deep maintenance.
- The effort put into maintaining these tools pays off through prolonged tool life, sustained performance, and reduced operational costs.
- Incorporating the maintenance practices detailed in this discussion ensures that your pneumatic tools remain valuable assets in your toolkit.
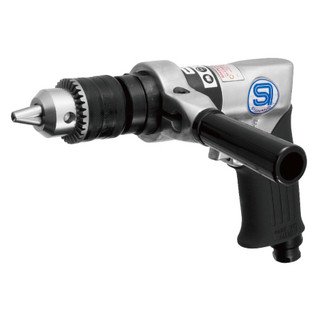
Introduction
Pneumatic tools are invaluable in workshops and industrial settings, revered for their power and efficiency. Yet, the secret to sustaining their optimal performance and extending their lifespan lies in routine and straightforward maintenance practices. This article will delve into the essential maintenance steps every pneumatic tool owner should follow, ensuring that these tools continue to operate at their best for years to come. We’ll also reference valuable insights from previous discussions on pneumatic tool care found on Pneumatic Tools and Accessories, such as the articles on proper maintenance and increasing productivity with these tools.
Understanding Pneumatic Tool Maintenance
Maintaining pneumatic tools is not just about fixing them when they break down; it’s about regular upkeep that prevents issues from arising. Consistent maintenance ensures that the tools perform efficiently and can significantly reduce the risk of failures that lead to downtime and costly repairs.
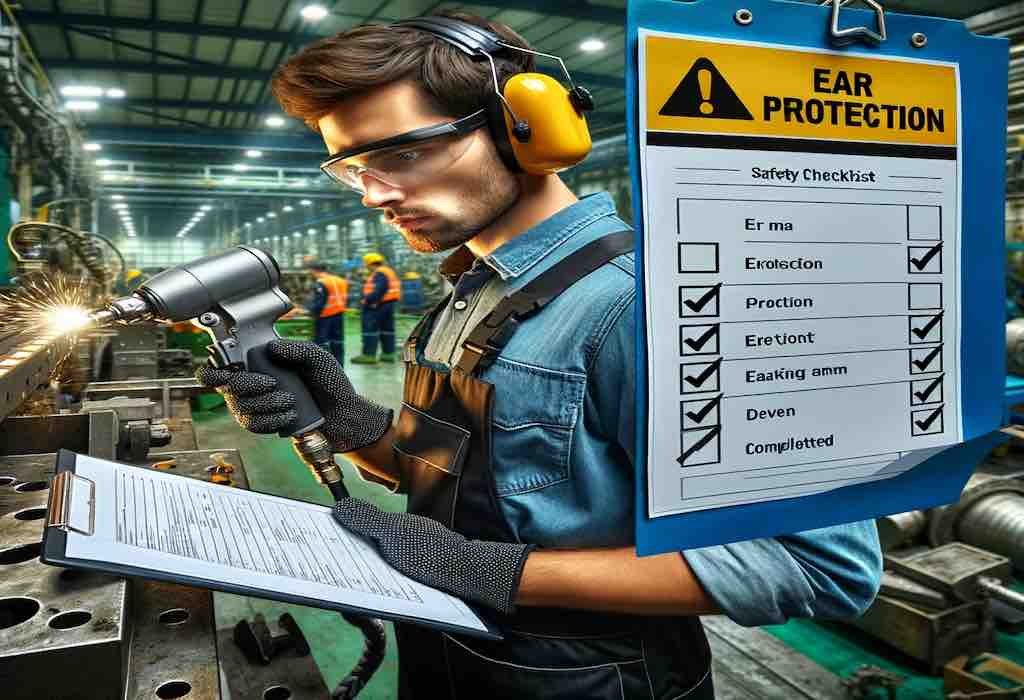
Key Areas of Focus in Pneumatic Tool Maintenance
- Lubrication: One of the most critical maintenance tasks for pneumatic tools involves proper lubrication. Most pneumatic tools require a few drops of oil in the air inlet before each use to keep the internal components running smoothly and to prevent rust and corrosion.
- Moisture Control: Compressed air can introduce moisture into pneumatic tools, which can lead to rust or freezing in colder climates. Draining the moisture from air compressors and using water separators or filters can mitigate this issue effectively.
- Regular Cleaning: Dust and debris can easily accumulate in pneumatic tools, especially in grinding, sanding, or drilling applications. Regular cleaning of the air intake vents and a quick wipe-down of the tool’s exterior help maintain its condition and functionality.
Practical Steps for Everyday Care
- Daily Inspections: Quick visual inspections can catch early signs of wear or damage. Checking for air leaks, worn seals, or loose components can prevent small issues from becoming major problems.
- Air Filter Maintenance: Just like any engine, the air compressor that powers pneumatic tools has an air filter that needs to be regularly cleaned or replaced. This ensures that clean, debris-free air powers the tool, which is crucial for its performance and longevity.
- Proper Storage: When not in use, pneumatic tools should be stored in a clean, dry environment. Proper storage protects the tools from environmental damage and ensures they are ready for use when needed next.
Let’s pause here. In the next segment, we will explore more advanced maintenance techniques, discuss the tools needed for maintaining your pneumatic equipment, and provide a step-by-step guide on conducting a thorough maintenance check. We’ll also look at how these practices tie into the broader context of pneumatic tool efficiency and longevity previously discussed in related articles on our site.
Advanced Maintenance Techniques and Essential Tools
As we delve deeper into the nuances of pneumatic tool care, it becomes clear that some maintenance tasks require more than just daily checks and basic cleaning. Advanced maintenance involves a deeper understanding of the tool’s mechanics and the adoption of practices that ensure every component functions optimally.
Comprehensive Servicing
- Seal and O-Ring Replacement: Over time, the seals and O-rings that protect the internal components of pneumatic tools from air leaks can degrade. Regularly checking and replacing these components is crucial to maintaining air pressure efficiency and tool performance.
- Hose Integrity Checks: The hoses are the lifelines of pneumatic tools. They should be regularly inspected for cracks, wear, or brittleness, especially near the connectors. Damaged hoses can dramatically reduce efficiency and are potential safety hazards, as they might lead to dangerous hose whips.
- Valve and Trigger Maintenance: Due to dirt buildup or lack of lubrication, the valves and triggers on pneumatic tools can become sticky or unresponsive. Cleaning and lubricating these parts can prevent operational issues and extend the tool’s life.
Essential Tools for Maintenance
To effectively maintain your pneumatic tools, you’ll need a set of specific tools designed for servicing:
- Air Tool Oil and Grease: Specialized lubricants designed for pneumatic tools help keep them running smoothly and prevent corrosion.
- Wrench Set and Screwdrivers: These are essential for disassembling tools to access internal components for deep cleaning or replacement.
- Air Line Filters and Dryers: Installing these in your air supply setup can significantly reduce moisture and debris, protecting your tools’ internal mechanisms.
- Calibration Equipment: For tools that require precise pressure settings, having calibration equipment can help ensure that they are operating within the necessary specifications.
Step-by-Step Guide to Conducting a Thorough Maintenance Check
Maintaining your pneumatic tools is an ongoing process. Here’s a simple step-by-step guide to conducting a thorough maintenance check:
- Disconnect the Tool: Safety first. Ensure the tool is disconnected from the air supply.
- Clean the Tool: Wipe down the exterior with a clean cloth. Compressed air blows out dust from the air intake and exhaust ports.
- Inspect for Wear: Check for visible wear or damage on the tool and its accessories. Look specifically at hoses, connections, and seals.
- Lubricate: Apply a few drops of air tool oil into the air inlet and run the tool briefly to distribute the oil internally.
- Test the Tool: Reconnect the tool to the air supply and test it to ensure it is operating correctly. Listen for unusual noises and monitor for consistent performance.
In the final section, we will summarize the crucial points covered in this article, answer some frequently asked questions about pneumatic tool maintenance, and guide how you can access further resources and products to help maintain your pneumatic tools effectively.
FAQs About Pneumatic Tool Maintenance
1. How often should I oil my pneumatic tools?
For best results, apply a few drops of air tool oil in the air inlet every time you use the tool to ensure proper lubrication and prevent internal wear.
2. What are the consequences of neglecting pneumatic tool maintenance?
Neglecting maintenance can lead to decreased tool performance, increased repair costs, premature tool failure, and potential safety hazards during operation.
3. Can I use any type of oil for my pneumatic tools?
No, it’s important to use air tool-specific oil. Other types of oil can contain detergents that may damage the tool’s internal components.
4. How do I know if my air tool needs service?
Indicators that your tool needs servicing include unusual noise, decreased performance, or excessive vibration. Also, if it’s been in use for an extended period without maintenance, it might be time for a check-up.
5. Is there a difference in maintenance needs between oil-free and oil-lubricated pneumatic tools?
Yes, oil-lubricated tools require regular oiling and more frequent maintenance to manage the oil levels and ensure the lubrication system works correctly. Oil-free tools generally need less maintenance in this area but still require regular cleaning and inspections.
Related Article:
Breathe Easy: Maintenance Best Practices for Pneumatic Tools
Durability and Longevity of Pneumatic Tools: Reliable Investments for Every Toolbox
Why Quality Matters: Investing in Premium Hand and Air Tools
Conclusion: Ensuring Pneumatic Tool Longevity Through Effective Maintenance
Proper maintenance of pneumatic tools is not just a requirement; it’s a practice that enhances both the efficiency and lifespan of these vital work instruments. Adhering to the simple yet crucial steps outlined in this article ensures that your tools remain in optimal condition, providing reliable performance and minimizing downtime due to repairs or failures.
Ready to enhance the performance and extend the lifespan of your pneumatic tools? Visit Pneumatic Tools and Accessories for a comprehensive selection of maintenance supplies, from specialized lubricants to replacement parts. Our experts are also on hand to provide advice and support, helping you keep your tools in top condition. Email us at sales@pneumatictoolz.com for more information on how to best care for your pneumatic tools and to explore our full range of products. Commit to the care of your tools today, and they will serve you reliably for years to come.