Key Takeaway
IoT integration in pneumatic tool systems offers new levels of efficiency, predictive maintenance, and data-driven decision making. By leveraging real-time data and advanced analytics, companies can significantly improve productivity, reduce downtime, and optimize their operations in ways that were previously impossible.
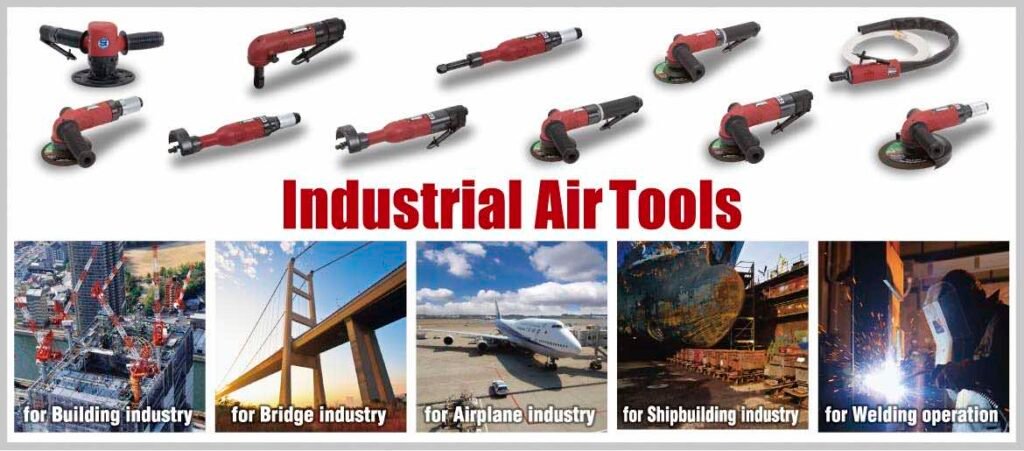
Introduction
The Internet of Things (IoT) has revolutionized numerous industries, and pneumatic tool systems is no exception. By integrating smart sensors, data analytics, and network connectivity into pneumatic systems, IoT is transforming how these tools are operated, maintained, and managed.
The Internet of Things (IoT) is revolutionizing modern pneumatic tool systems by enabling enhanced connectivity, monitoring, and control across industrial operations. With IoT integration, pneumatic tools can now be equipped with sensors and connected to a central network, allowing real-time data collection on tool performance, usage patterns, and maintenance needs. This connectivity facilitates predictive maintenance, reducing downtime by alerting operators before failures occur. Additionally, IoT-enabled systems can optimize energy efficiency by monitoring air pressure and adjusting tool operations for optimal performance. Overall, IoT in pneumatic tool systems leads to smarter, more efficient, and safer industrial environments, offering significant improvements in productivity and cost savings.
This article explores the profound impact of IoT on modern pneumatic tool systems and the benefits it brings to manufacturers and end-users alike.
Understanding IoT in Pneumatic Systems
IoT in pneumatic systems involves the integration of smart sensors, actuators, and communication technologies into pneumatic tools and their associated infrastructure. This connectivity allows for real-time monitoring, data collection, and remote control of pneumatic equipment.
Components of an IoT-Enabled Pneumatic System
- Smart Sensors: Measure various parameters such as air pressure, temperature, vibration, and energy consumption.
- Actuators: Allow for remote control and adjustment of tool settings.
- Gateway Devices: Facilitate communication between tools and the central system.
- Cloud Platforms: Store and process data collected from pneumatic tools.
- Analytics Software: Analyze data to provide insights and predictions.
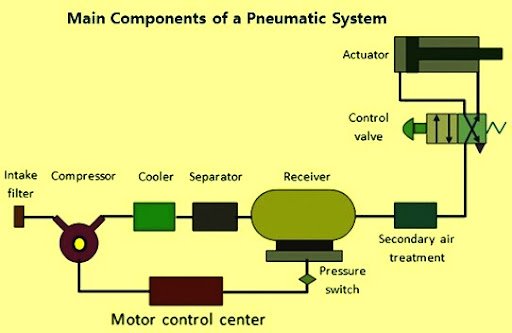
Benefits of IoT in Pneumatic Tool Systems
1. Real-Time Monitoring and Control
IoT enables continuous monitoring of pneumatic tool systems performance, allowing operators to:
- Track air pressure and flow rates in real-time
- Monitor tool temperature and vibration levels
- Adjust tool settings remotely for optimal performance
Case Study: A large automotive manufacturing plant implemented IoT-enabled pneumatic tools, resulting in a 20% increase in overall equipment effectiveness (OEE) due to real-time adjustments and optimizations.
2. Predictive Maintenance
By analyzing data patterns, IoT systems can predict when maintenance is needed, helping to:
- Prevent unexpected breakdowns
- Reduce downtime
- Optimize maintenance schedules
Statistic: Companies implementing IoT-based predictive maintenance have reported up to 50% reduction in equipment downtime and 20-25% savings in maintenance costs.
3. Energy Efficiency
IoT systems can optimize energy usage by:
- Identifying and alerting about air leaks
- Adjusting compressor output based on demand
- Providing insights for more efficient tool usage
4. Enhanced Safety
IoT can improve workplace safety by:
- Monitoring tool usage patterns to prevent operator fatigue
- Alerting supervisors to abnormal tool behavior
- Ensuring tools are operated within safe parameters
5. Quality Control
IoT-enabled pneumatic tools can contribute to better quality control by:
- Ensuring consistent torque and pressure application
- Tracking and recording tool operations for quality assurance
- Alerting operators to deviations from specified parameters
6. Data-Driven Decision Making
The wealth of data provided by IoT systems allows managers to:
- Analyze tool usage patterns to optimize workflows
- Make informed decisions about equipment investments
- Identify bottlenecks in production processes
Implementing IoT in Pneumatic Systems
1. Assessment and Planning
- Evaluate current pneumatic system and identify areas for improvement
- Define specific goals for IoT implementation (e.g., energy savings, downtime reduction)
- Develop a phased implementation plan
2. Selecting the Right IoT Solution
- Choose sensors and actuators compatible with existing equipment
- Select a robust and scalable IoT platform
- Ensure the chosen solution meets industry-specific requirements (e.g., ATEX certification for explosive environments)
3. Integration and Installation
- Install sensors and actuators on pneumatic tools and compressors
- Set up gateway devices and network infrastructure
- Integrate the IoT system with existing management software (e.g., ERP, MES)
4. Data Management and Analytics
- Establish data collection and storage protocols
- Implement analytics tools for data interpretation
- Train staff on data analysis and system management
5. Continuous Improvement
- Regularly review system performance and adjust as needed
- Stay updated on new IoT technologies and integrate when beneficial
- Continuously train staff to maximize the benefits of the IoT system
Challenges in Implementing IoT in Pneumatic Systems
- Initial Costs: The upfront investment for IoT implementation can be significant.
- Data Security: Ensuring the security of sensitive operational data is crucial.
- Integration with Legacy Systems: Older pneumatic tools may require retrofitting or replacement.
- Skill Gap: Staff may need training to effectively use and maintain IoT systems.
- Standardization: Lack of universal standards in IoT can lead to compatibility issues.
Future Trends in IoT for Pneumatic Tools
- Artificial Intelligence and Machine Learning: Enhanced predictive capabilities and autonomous system optimization.
- 5G Integration: Faster, more reliable communication for real-time control and monitoring.
- Edge Computing: Processing data closer to the source for quicker response times and reduced bandwidth usage.
- Digital Twins: Creating virtual models of pneumatic systems for advanced simulation and optimization.
- Augmented Reality Integration: Using AR for maintenance guidance and training.
Frequently Asked Questions
1. How does IoT improve the energy efficiency of pneumatic systems?
IoT enables real-time monitoring of air consumption, helps detect leaks quickly, and allows for demand-based compressor control, all contributing to significant energy savings.
2. What kind of return on investment (ROI) can be expected from implementing IoT in pneumatic systems?
While ROI varies, many companies report 20-30% reductions in energy costs and maintenance expenses within the first year of implementation.
3. How does IoT in pneumatic tools contribute to workplace safety?
IoT systems can monitor tool usage patterns to prevent operator fatigue, alert to unsafe operating conditions, and ensure tools are used within safe parameters, significantly reducing the risk of accidents.
4. Can existing pneumatic tools be retrofitted with IoT capabilities?
Yes, many existing tools can be retrofitted with IoT sensors and communication modules. However, the extent of retrofitting depends on the specific tool and desired IoT capabilities.
5. How is data security ensured in IoT-enabled pneumatic systems?
Data security is maintained through encryption, secure communication protocols, regular software updates, and access control measures. It’s crucial to work with reputable IoT providers who prioritize security.
Conclusion
The integration of IoT into pneumatic tool systems represents a significant leap forward in industrial technology. By providing real-time insights, enabling predictive maintenance, and optimizing performance, IoT is helping companies achieve new levels of efficiency, productivity, and safety. As the technology continues to evolve, we can expect even more innovative applications that will further transform the capabilities of pneumatic tools.
Ready to revolutionize your pneumatic tool systems with cutting-edge IoT technology? At Pneumatic Tools and Accessories, we’re at the forefront of integrating IoT solutions with pneumatic systems.
Visit our website at pneumatictoolz.com to explore our range of IoT-enabled pneumatic tools and smart compressor systems. Our expert team can guide you through the process of upgrading your existing setup or implementing a new, fully integrated IoT pneumatic system.
For a personalized consultation on how IoT can optimize your specific pneumatic operations, contact us today at sales@pneumatictoolz.com. Let’s work together to bring your pneumatic systems into the future of industry