Pneumatic tools are all powered by compressed air, they have been a cornerstone of industrial and professional applications for over a century. These versatile and powerful tools offer unique advantages in terms of performance, durability, and efficiency. For beginners entering the world of air-powered equipment, understanding the basics of pneumatic tools is crucial for proper selection, safe operation, and effective maintenance. This comprehensive guide aims to demystify pneumatic tools, providing novices with a solid foundation in air-powered technology and its applications.
Key Takeaways
- Pneumatic tools operate using compressed air, offering high power-to-weight ratios and the ability to work continuously without overheating.
- A basic pneumatic system consists of an air compressor, air preparation units, distribution system, and the tools themselves.
- Proper safety measures, including personal protective equipment and regular maintenance, are crucial when working with pneumatic tools.
- Understanding air consumption (CFM) and pressure requirements (PSI) is essential for selecting the right tools and compressor.
- Regular maintenance of both the tools and the air supply system is key to ensuring longevity, efficiency, and safety.
What Are Pneumatic Tools?
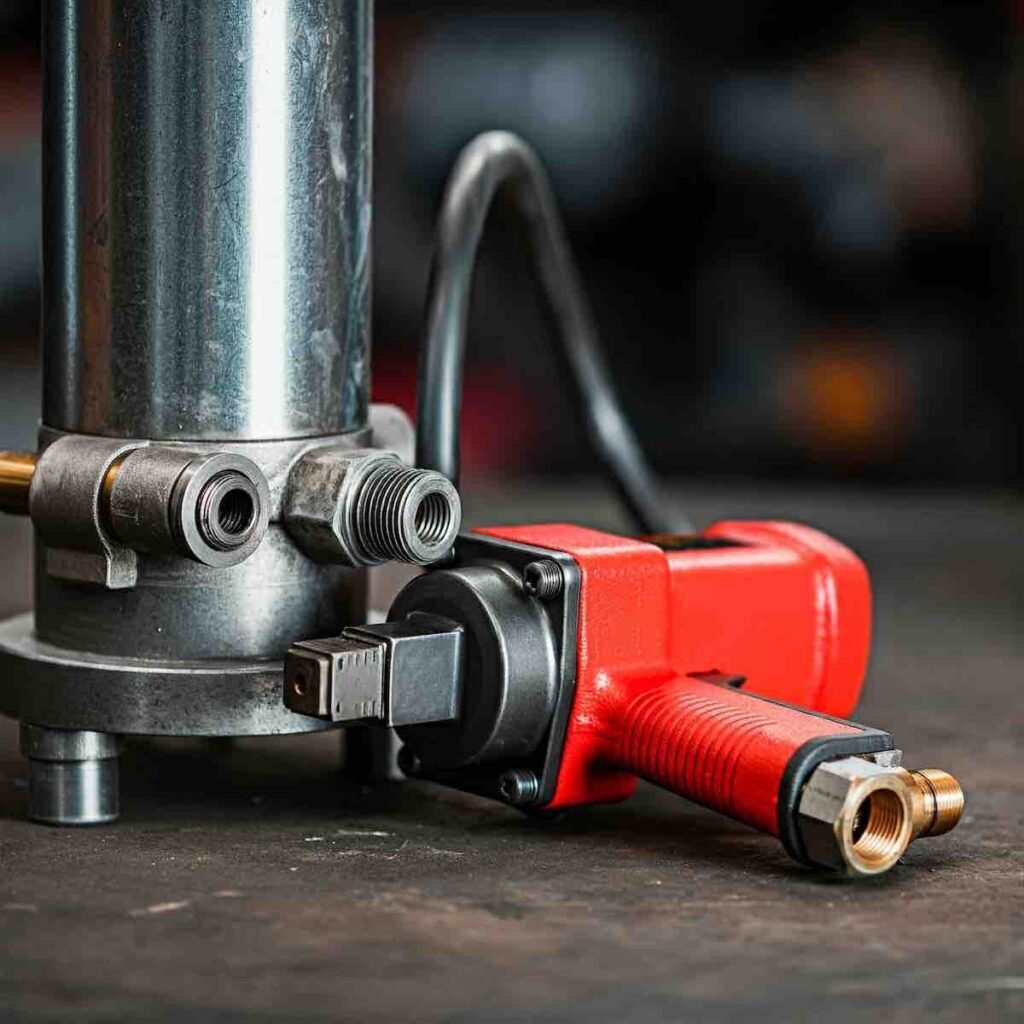
Pneumatic tools, also known as air tools or air-powered tools, are a category of power tools that use compressed air as their energy source. This compressed air drives a motor or piston within the tool, converting air pressure into mechanical motion to perform various tasks.
Basic Principles of Operation
- Air Compression: An air compressor pressurizes air, storing it in a tank.
- Air Distribution: Compressed air is delivered to the tool through hoses.
- Energy Conversion: The tool converts the energy of compressed air into mechanical work.
- Exhaust: Used air is expelled from the tool, often through a muffler to reduce noise.
Advantages of Pneumatic Tools
- High power-to-weight ratio
- Ability to operate continuously without overheating
- Safe for use in wet or potentially explosive environments
- Generally more durable and require less maintenance than electric tools
- Can deliver constant torque or force output
Common Types of Pneumatic Tools
- Impact Wrenches: For high-torque applications like loosening lug nuts
- Nail Guns: Used in construction and woodworking for rapid fastening
- Air Hammers: For breaking up concrete or rock in construction and mining
- Sanders and Grinders: For surface preparation and finishing in manufacturing and automotive work
- Spray Guns: Used in painting and coating applications
- Drills: For precise hole-drilling in various materials
- Air Compressors: While not a tool itself, it’s the heart of any pneumatic system
Components of a Pneumatic System
Understanding the key components of a pneumatic system is crucial for anyone looking to work with air-powered tools.
Air Compressor
The air compressor is the power source of the pneumatic system. It takes in ambient air, compresses it to high pressure, and stores it in a tank for use.
Key Factors:
- Cubic Feet per Minute (CFM): Measures the volume of air the compressor can deliver
- Pounds per Square Inch (PSI): Indicates the pressure at which the air is delivered
- Tank Size: Determines how long tools can run before the compressor needs to cycle on
Air Preparation Units
These components ensure that the compressed air is clean, dry, and at the right pressure for the tools.
Components include:
- Air Filter: Removes particulates from the air
- Regulator: Controls the air pressure delivered to the tool
- Lubricator: Adds oil to the air stream for tool lubrication (if required)
Distribution System
The distribution system delivers compressed air from the compressor to the tools.
Key Components:
- Air Hoses: Flexible tubes that carry the compressed air
- Fittings and Couplers: Connect hoses to tools and the compressor
- Manifolds: Distribute air to multiple tools or work stations
Pneumatic Tools
The end-use devices that convert compressed air into mechanical work.
Selecting the Right Pneumatic Tools
Choosing the appropriate pneumatic tools depends on several factors:
- Air Consumption (CFM): Ensure your compressor can supply enough air volume for the tool.
- Operating Pressure (PSI): Match the tool’s required pressure to your compressor’s output.
- Duty Cycle: Consider how often and for how long the tool will be used.
- Specific Job Requirements: Choose tools designed for your particular applications.
- Ergonomics: Consider tool weight, balance, and grip for user comfort.
- Noise Level: Some pneumatic tools can be loud; consider noise-reduced options if necessary.
Safety Considerations
Safety is paramount when working with pneumatic tools. Key safety measures include:
- Personal Protective Equipment (PPE):
- Safety glasses or face shield
- Hearing protection
- Steel-toed boots
- Work gloves
- Proper Training: Ensure all users are trained in the safe operation of pneumatic tools.
- Tool Inspection: Regularly check tools for wear, damage, or loose parts.
- Correct Air Pressure: Use tools only at their rated pressure to prevent damage or injury.
- Secure Work Pieces: Ensure materials being worked on are properly secured.
- Proper Tool Storage: Store tools in a clean, dry place when not in use.
- Compressed Air Safety: Never use compressed air to clean clothing or skin.
Maintenance and Care
Proper maintenance is crucial for the longevity, efficiency, and safe operation of pneumatic tools.
Daily Maintenance
- Inspect tools and hoses for damage before each use
- Clean tools after use, removing any debris or moisture
- Lubricate tools according to manufacturer’s instructions
Regular Maintenance
- Check and clean air filters on the compressor and preparation units
- Drain moisture from the compressor tank and air lines
- Tighten any loose fittings or connections
- Replace worn parts as needed
Compressor Maintenance
- Change oil as recommended by the manufacturer
- Clean or replace air intake filter regularly
- Check belt tension (for belt-driven compressors)
- Inspect safety valves and gauges for proper operation
Troubleshooting Common Issues
Understanding basic troubleshooting can help resolve common issues with pneumatic tools:
- Low Power Output:
- Check for air leaks in hoses or connections
- Ensure proper air pressure from the compressor
- Clean or replace air filters
- Tool Not Operating:
- Verify air supply is connected and compressor is running
- Check for blockages in the air inlet
- Inspect for internal damage or worn parts
- Excessive Noise:
- Check for loose parts or connections
- Inspect muffler for damage
- Ensure proper lubrication
- Air Leaks:
- Tighten loose connections
- Replace damaged hoses or fittings
- Check seals and O-rings for wear
Important Information
- The global pneumatic tools market was valued at $22.9 billion in 2020 and is projected to reach $36.5 billion by 2027, reflecting the continued importance of these tools in various industries.
- Pneumatic tools typically operate at pressures ranging from 70 to 120 PSI, with some specialized tools reaching up to 300 PSI.
- Proper maintenance can extend the life of pneumatic tools to 20-30 years, significantly longer than many electric alternatives.
- Air compressors account for approximately 10% of all industrial electricity usage in the United States, highlighting the importance of energy efficiency in pneumatic systems.
- The use of variable speed drive (VSD) compressors can reduce energy consumption by up to 35% compared to traditional fixed-speed compressors.
Frequently Asked Questions
What’s the difference between CFM and PSI in pneumatic tools?
CFM (Cubic Feet per Minute) measures the volume of air flow, while PSI (Pounds per Square Inch) measures air pressure. Both are important: CFM determines how much air your tool needs to operate continuously, while PSI indicates the force with which the air is delivered.
Do all pneumatic tools require oil?
Not all pneumatic tools require oil. Many modern tools are designed to be oil-free, which can be beneficial in environments where oil contamination is a concern. However, some tools still require regular oiling for optimal performance and longevity. Always check the manufacturer’s recommendations.
Can I use any air compressor with any pneumatic tool?
Not necessarily. You need to match the air compressor’s output (in terms of CFM and PSI) to the tool’s requirements. Using a compressor that can’t supply enough air volume or pressure will result in poor tool performance.
How often should I drain my air compressor?
It’s generally recommended to drain your air compressor’s tank daily if used regularly. This prevents moisture buildup which can lead to internal rusting and contamination of your air supply.
Are pneumatic tools safer than electric tools?
Pneumatic tools have some safety advantages, such as no risk of electric shock and the ability to operate in wet environments. However, they come with their own safety considerations, such as the potential for high-pressure air injuries. Both types of tools can be safe when used properly with appropriate safety measures.
Related Content
- Understanding Pneumatic Tools: A Comprehensive Guide
- How to Properly Maintain and Extend the Lifespan of Your Pneumatic Tools
- Comparing Pneumatic vs. Electric Tools: Pros and Cons
- The Environmental Benefits of Using Pneumatic and Air-Powered Tools
Tired of slow, cumbersome tools that hold you back? Upgrade to the speed and reliability of pneumatic power! Explore our range of pneumatic tools at pneumatictoolz.com and discover the difference. Have questions? Our team at sales@pneumatictoolz.com is ready to assist you.